Ytron
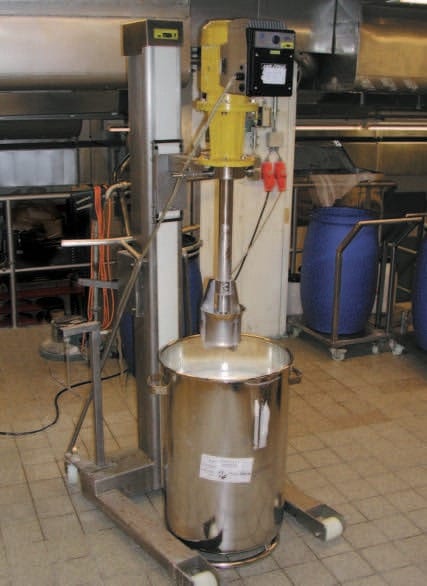
When manufacturing emulsions, YTRON technology plays an important role. To make this clear, we would first like to define the term emulsion. This is a mixture of raw materials that actually cannot be mixed. For example, if you mix oil and water, although both liquids initially blend together to certain extent, if the container is allowed to stand for a while both substances will slowly separate. Emulsifiers are used as an aid. They accumulate on the interfaces of fat and water drops, align their polar groups towards the water and orient the non-polar groups to the fat phase. In this manner both phases combine as a bridge, contributing to the effective stabilisation of the emulsion. An important role for long term stability is also played by stabilisers, such as polymers (xanthan gum, carbomers, gellan gum, caesalpinia spinosa gum, carrageenan, modified acrylate, cellulose types etc.), which build up a three-dimensional network in the product, thus ensuring sufficient long term stabilisation. YTRON-ZC power dissolving systems are highly suitable for dispersing this usually difficult to wet dry matter.
YTRON technology and its advantages
When mixing liquids, conventional mixers usually have clear disadvantages: the blending is often defective, unwanted air is sucked in, there is vortex formation and frequently very strong gas formation. This can have negative consequences for the product quality: heat transfer problems, changes of colour and oxidations are just some examples here. In many cases the contents of the container also does not fully circulate and so-called flow dead zones form on the baffles in the tank. Furthermore, the entire process takes a long time and is thus not profitable these days.
Advantages of this gentle manufacturing technology
All this looks very different with the help of YTRON technology. When manufacturing emulsions, YTRON technology provides homogeneous blending, quickly and intensively circulates the entire contents of the container and generates an exclusively axial flow. Negative side effects, such as those caused by conventional mixers, are effectively prevented by YTRON technology. This includes above all unwanted air being sucked in, sedimentation and so-called floating, i.e. the powder floating on the top. No baffle is needed in the tank either. Instead, with YTRON technology flow deflectors are integrated in the stator.
Due to the very short times it spends in the Y blender head, YTRON technology is also very gentle on the product. Only the running product comes into contact with the rotor and air cushions prevent the product coming into contact with the seal. YTRON technology also convinces not least through an enormous time saving. The entire process runs in much less time, clearly improving cost-effectiveness.
YTRON technology generally works in three phases. Firstly, all solid particles lying on the base are raised by the jet emitted down to the base of the container. Then, the solid particles are spread homogenously within a matter of seconds, without any sedimentation and without sucking in any air.
The YTRON technology stator with integrated flow deflectors then generates an axially directed jet across the entire base of the container. This flow guarantees an absolutely homogeneous product.
In comparison, the procedure without YTRON technology: here the solids are initially stirred up from the base after switching on. But the proportion of radially effective forces cannot keep the particles floating. After just a short time the first vortex reaches the rotor blade. The radial flow thus tends to separate the components, in contrast to what happens with YTRON technology. In this conventional procedure, for design reasons achieving a homogeneous mix without sucking in air is as good as impossible.
Polymers, colour pigments or other highly viscous products can be spread in the product quickly and effectively. This significantly reduces swelling and homogenisation times.
Conclusion: YTRON technology is currently the leader in efficiency and cost-effectiveness
With its many advantages YTRON technology has become an indispensable constituent of cosmetics manufacturing. YTRON technology works gently with the product, as well as quickly, effectively and absolutely reliably.